Belotti Integrale
Cellule robotique modulaire capable d'intégrer des systèmes et des langages CNC et robotiques et de s'intégrer dans une ligne de production hautement automatisée.
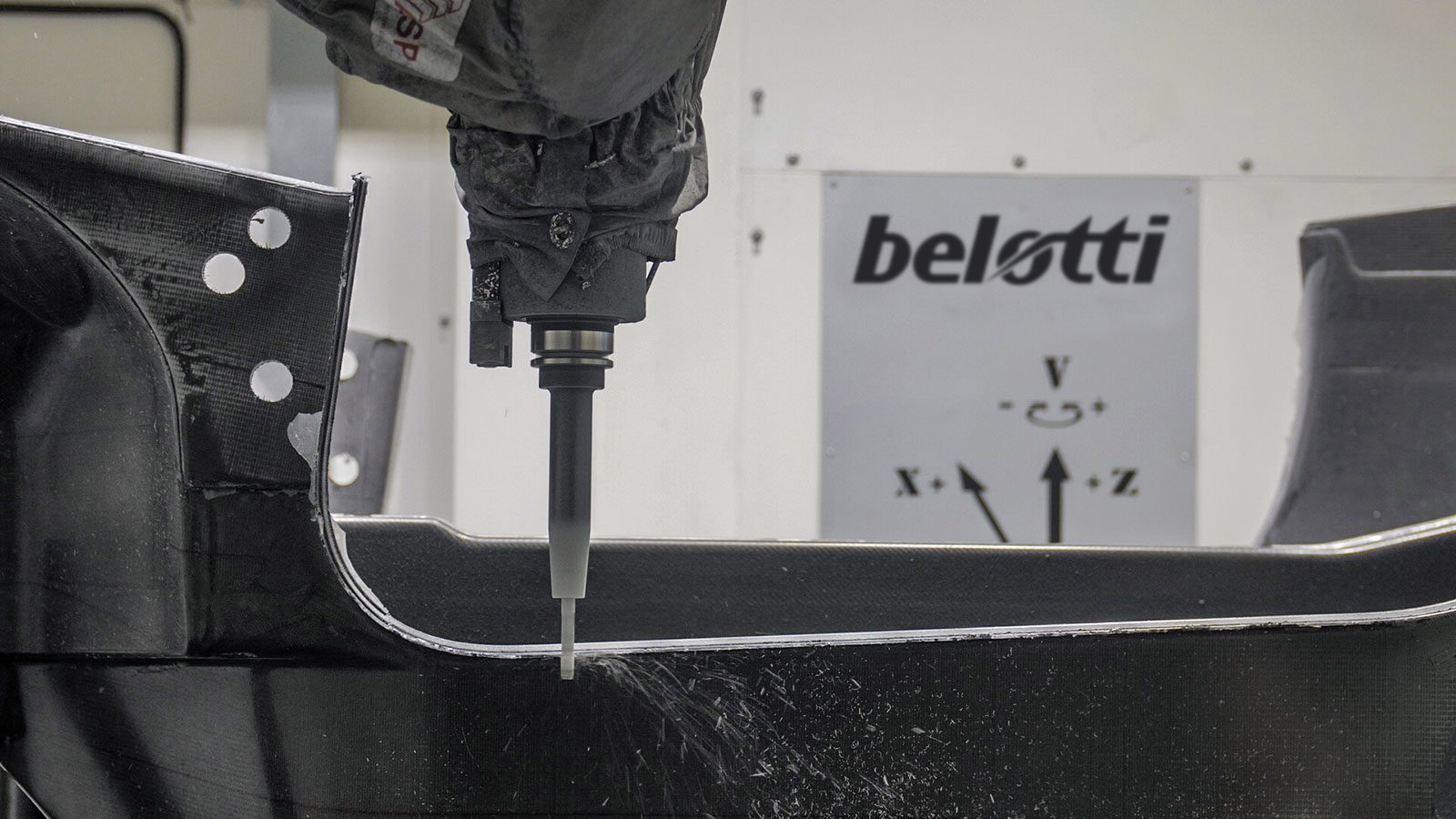
Optimiser le cycle de production, augmenter la production grâce à un niveau d’automatisation de l’usine toujours plus élevé. Pour répondre au mieux aux besoins du secteur automobile, Belotti a développé, en étroite collaboration avec KUKA et Siemens, Belotti Integrale, une cellule robotisée à deux niveaux pour l’usinage des matériaux avancés (carbone, Kevlar, alliages légers).
Description
Défis et objectifs du projet:
- Assurer la flexibilité et la facilité d’utilisation;
- Optimiser les performances et l’efficacité de la production;
- Faire partie d’une ligne automatisée, dans un contexte de Flexible Manufacturing Systems.
La ligne pilote Belotti Integrale a été installée comme module de soutien dans la ligne d’assemblage du super SUV Urus d’Automobili Lamborghini à Sant’Agata Bolognese, une marque phare du secteur automobile de luxe appartenant à l’Allemand Audi (groupe Volkswagen).
Belotti Integrale est en fait une cellule robotisée qui s’intègre aux machines CNC traditionnelles déjà présentes dans l’usine de production du client et qui communique avec ses systèmes de chargement/déchargement de palettes et de transport/transfert de matériel.
Les robots anthropomorphes de haute précision à l’intérieur de la machine garantissent un niveau élevé de précision et d’attention aux détails dans le détourage, le perçage et le rodage des matériaux composites (tels que la fibre de carbone) et des composants en alliage d’aluminium utilisés dans le secteur de l’automobile haut de gamme.
Au niveau inférieur, une table mobile située au centre de la machine est desservie par deux navettes latérales qui prennent la palette dans le système existant et l’amènent dans la cellule. Des portes automatiques étanches à la poussière s’ouvrent et se ferment rapidement à proximité de la navette.
Ensuite, l’usinage des matériaux s’effectue via un premier robot KUKA (modèle QUANTEC KR 270 R2700) suspendu au plafond pour pouvoir accéder à plusieurs points de la cellule elle-même. L’usinage est également facilité par la table rotative, qui permet de disposer les différentes faces de la pièce devant le robot. L’usinage des corps en matériaux composites comprend principalement le fraisage, le perçage, le détourage et toutes les autres opérations spéciales demandées par le client, avec la possibilité d’installer des outils spécifiques pour automatiser des processus qui étaient auparavant effectués manuellement.
Pour des raisons d’espace, un étage surélevé a été créé pour l’outillage, qui est habituellement placé au sol. Au niveau supérieur, un deuxième robot KUKA (modèle KR 30) s’occupe précisément des fonctions de changement d’outil et de mesure. L’échange avec le premier robot s’effectue par une ouverture dédiée dans le plafond. Le deuxième robot accède à un magasin d’échange « rapide » à 36 positions pour prendre les outils utilisés pendant l’usinage et, pendant les temps morts, effectue un usinage secondaire : il déplace les outils vers le magasin à chaîne « lent », pour les soutenir et les stocker, afin qu’ils soient toujours disponibles, et il prépare les outils pour l’opération d’usinage suivante.
De plus, le deuxième robot récupère l’outil qui vient d’être utilisé sur le robot du niveau inférieur, reconnaît ses spécifications, détecte ses dimensions et le place dans le magasin ou dans un autre endroit dédié s’il est trop usé ou cassé. Le chargement principal des outils se fait manuellement : l’opérateur, en fonction des cycles de travail, précharge un certain nombre d’outils dans la machine, en utilisant un élévateur spécial pour les amener au niveau supérieur, où ils seront ensuite manipulés par le robot KUKA, qui les prend, les lit pour confirmation et les place dans l’emplacement dédié. En cas de besoin, la machine peut être commandée par l’opérateur de l’étage inférieur, tandis que l’accès à l’étage supérieur se fait par une échelle, pour la maintenance et l’inspection éventuelle. En fait, l’outillage hautement personnalisé et la gestion des outils visent à faire fonctionner la machine de manière autonome, sans personnel, même pendant de longues périodes.
La réalisation de l’ensemble de la solution Belotti a été rendue possible grâce à l’ouverture et à la flexibilité des CNC Sinumerik One de Siemens, qui ont permis de « contrôler » et de programmer facilement les opérations très complexes des deux robots KUKA, tout en gérant leurs diagnostics et en permettant au client final de disposer d’un point d’accès unique pour l’assistance à distance nécessaire.
La complexité de cette solution Belotti est liée précisément au très haut degré d’automatisation qui la caractérise et qui répond au besoin du client d’optimiser le cycle de production, en augmentant la productivité des pièces usinées d’environ 30%.
La machine, qui peut être facilement insérée dans un processus de production existant, permet un haut degré de modularité. En effet, le client peut choisir dès la phase de négociation ou ajouter dans un deuxième temps les modules qui répondent le mieux à ses besoins. Par rapport aux systèmes fermés traditionnels, Belotti Integrale permet donc une mise au jour plus facile de la ligne, en ajoutant des modules selon les fonctions requises ou les nouveaux besoins de production. En effet, chaque module représente une fonction, un traitement spécifique que le client a l’intention d’introduire. Cette caractéristique permet en outre une plus grande flexibilité, ainsi que la possibilité de faire évoluer sa propre ligne sans compromettre les investissements antérieurs. Un concept très similaire à celui des logiciels : à partir d’un module de base, il est possible de personnaliser le produit selon les spécifications du client et de le maintenir constamment à jour.
Belotti Integrale est l’une des premières applications au monde à intégrer la robotique et la CNC : les robots sont en effet contrôlés par la commande numérique de Siemens via la fonctionnalité Sinumerik Integrate Run MyRobot, ce qui permet au client de programmer le robot avec le langage ISO classique typique des machines-outils.
Ceci a été rendu possible grâce à la collaboration de deux grands acteurs mondiaux tels que KUKA et Siemens, avec la définition d’une interface permettant l’échange de données entre les deux systèmes associés et le travail de Belotti, l’union finale qui a intégré ces mêmes systèmes et langages au sein de sa machine à commande numérique.
Le CNC Sinumerik de Siemens, capable de dialoguer parfaitement avec le logiciel de commande KUKA pour la gestion des robots, était la solution idéale pour réaliser l’intégration entre la technologie CNC et les robots : une solution d’automatisation intelligente pour le bénéfice total du client.
Contactez-nous pour obtenir des plus amples informations techniques ou commerciales ou pour demander une présentation en ligne.
Contactez-nous pour des informations sur les produits, une assistance technique ou des pièces de rechange