Belotti integrale
Modulare Roboterzelle, die in der Lage ist, CNC- und Robotersysteme und -sprachen zu integrieren und sich in eine hochautomatisierte Produktionslinie einzufügen.
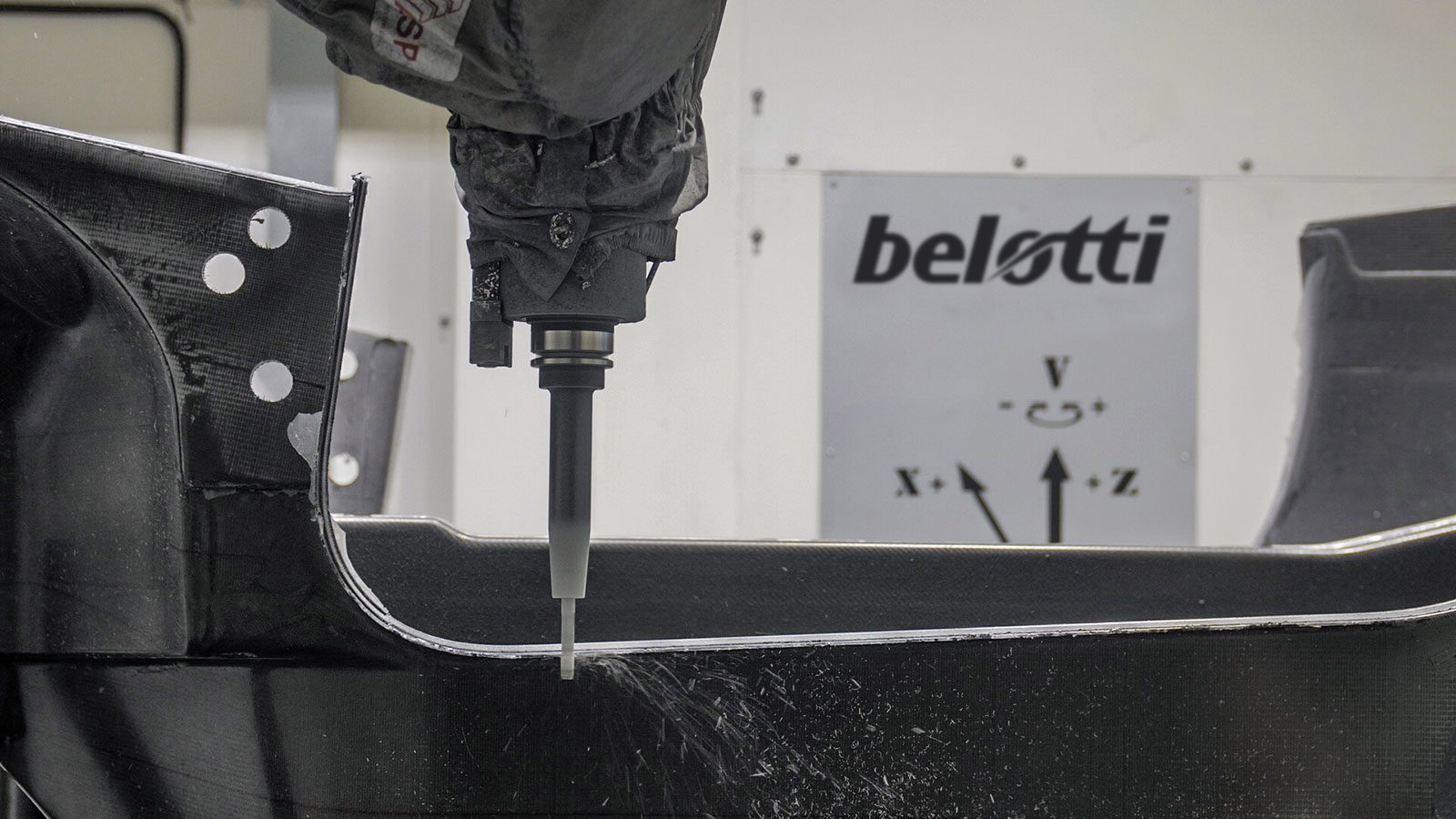
Optimierung des Produktionszykluses, Steigerung der Produktion durch einen immer höheren Automatisierungsgrad der Anlagen. Um den Anforderungen des Automobilsektors bestmöglich gerecht zu werden, hat Belotti in enger Zusammenarbeit mit KUKA und Siemens die Belotti Integrale entwickelt, eine zweistufige Roboterzelle für die Verarbeitung fortschrittlicher Materialien (Carbon, Kevlar, Leichtmetall).
Beschreibung
Herausforderungen und Ziele des Projekts
- Gewährleistung von Flexibilität und Benutzerfreundlichkeit;
- die Leistung und die Produktionseffizienz zu optimieren;
- im Rahmen von flexiblen Fertigungssystemen Teil einer automatisierten Linie zu werden.
Die Pilotlinie Belotti Integrale wurde als Unterstützungsmodul in der Montagelinie des Super-Geländewagens Urus von Automobili Lamborghini in Sant’Agata Bolognia installiert.Eine führenden Luxus-Automobilmarke im Besitz des deutschen Audi-Konzerns (Volkswagen-Gruppe).
Belotti Integrale ist in der Tat eine Roboterzelle, die sich in die traditionellen CNC-Maschinen integriert, die bereits in der Produktionsanlage des Kunden vorhanden sind, und die mit den Systemen zum Be- und Entladen von Paletten und zum Transport von Ausrüstungen kommuniziert.
Die hochpräzisen anthropomorphen Roboter im Inneren der Maschine garantieren ein hohes Maß an Genauigkeit und Detailtreue beim Beschneiden, Bohren und Honen von Verbundwerkstoffen (z. B. Kohlefaser) und Aluminiumlegierungen, die im High-End-Automobilsektor verwendet werden.
Auf der unteren Ebene wird ein mobiler Tisch in der Mitte der Maschine von zwei seitlichen Shuttles bedient, die die Palette vom bestehenden System abholen und in die Zelle bringen. Es gibt staubdichte automatische Türen, die sich in der Nähe des Shuttles schnell öffnen und schließen.
Anschließend werden die Materialien von einem ersten KUKA-Roboter (Modell QUANTEC KR 270 R2700) bearbeitet, der von der Decke herabhängt, um mehrere Stellen in der Zelle zu erreichen. Die Bearbeitung wird durch den Drehtisch erleichtert, der die verschiedenen Flächen des Werkstücks vor dem Roboter positionieren kann. Die wichtigsten Bearbeitungen an Verbundwerkstoff-Karosserien sind Fräsen, Bohren, Entgraten und alle anderen vom Kunden geforderten Sonderbearbeitungen, wobei die Möglichkeit besteht, spezielle Werkzeuge zu installieren, um diese Bearbeitungen zu automatisieren, die früher manuell durchgeführt wurden.
Aus Platzgründen wurde für die Werkzeuge, die sich normalerweise auf dem Boden befinden, eine erhöhte Ebene geschaffen. Auf dieser oberen Ebene arbeitet ein zweiter KUKA-Roboter (Typ KR 30), der den Werkzeugwechsel und die Messfunktionen übernimmt. Der Austausch mit dem ersten Roboter erfolgt durch eine spezielle Öffnung in der Decke. Der zweite Roboter greift auf ein Schnellwechselmagazin mit 36 Positionen zu, um die während der Bearbeitung verwendeten Werkzeuge aufzunehmen und in den Stillstands Zeiten eine Nachbearbeitung durchzuführen: d.h.es verschiebt die Werkzeuge in das „langsame“ Kettenmagazin, um sie zu lagern und zu speichern, damit sie immer verfügbar sind, und bereitet die Werkzeuge für die nächste Bearbeitung vor. Außerdem nimmt der zweite Roboter das Werkzeug, das gerade seine Arbeit beendet hat, vom Roboter in der unteren Etage auf, erkennt seine Spezifikationen, ermittelt seine Abmessungen und legt es in das Magazin oder an einen anderen dafür vorgesehenen Platz, wenn es zu stark abgenutzt oder gebrochen ist. Die Hauptbeladung der Werkzeuge erfolgt manuell: Der Bediener lädt je nach Arbeitszyklus eine bestimmte Anzahl von Werkzeugen in die Maschine vor und bringt sie mit einem speziellen „Aufzug“ in die obere Ebene, wo sie dann vom KUKA-Roboter gehandhabt werden, der sie aufnimmt, zur Bestätigung einliest und an dem dafür vorgesehenen Platz ablegt. Bei Bedarf kann die Maschine vom Bediener in der unteren Etage gesteuert werden, während der Zugang zur oberen Etage für Wartungs- und Inspektionszwecke über eine Treppe erfolgt. Das Ziel der hochgradig angepassten Werkzeuge und des Managements ist es, dass die Maschine autonom und mannarm arbeitet, auch über längere Zeiträume hinweg. Die Umsetzung der gesamten Belotti-Lösung wurde durch die Offenheit und Flexibilität der Siemens Sinumerik 840D sl CNCs ermöglicht, die es erlaubten, die hochkomplexen Operationen der beiden KUKA-Roboter einfach zu „steuern“ und zu programmieren, ihre Diagnose zu verwalten und dem Endkunden einen einzigen Zugangspunkt für die notwendige Fernunterstützung zu bieten.
Die Komplexität dieser Belotti-Lösung ist genau auf den sehr hohen Automatisierungsgrad zurückzuführen, der sie auszeichnet und der dem Bedürfnis des Kunden nach Optimierung des Produktionszyklus entspricht, indem er die Produktivität der bearbeiteten Teile um etwa 30 % erhöht.
Die Maschine, die sich leicht in einen bestehenden Produktionsprozess einfügen lässt, ermöglicht ein hohes Maß an Modularität. Der Kunde kann nämlich während der Planungsphase die Module auswählen oder später hinzufügen, die seinen Bedürfnissen am besten entsprechen. Im Vergleich zu herkömmlichen geschlossenen Systemen ermöglicht Belotti Integrale daher eine einfachere Aktualisierung der Linie, indem Module entsprechend den erforderlichen Funktionen oder neuen Produktionsanforderungen hinzugefügt werden. Jedes Modul steht für eine Funktion, einen bestimmten Prozess, den der Kunde einführen möchte. Diese Eigenschaft ermöglicht zudem eine größere Flexibilität und die Möglichkeit, die eigene Linie weiterzuentwickeln, ohne frühere Investitionen zunichtezumachen. Ein Konzept, das dem von Software sehr ähnlich ist: Aus einem Basismodul kann ein auf die erforderlichen Funktionen und Bedürfnisse des Kunden zugeschnittenes Produkt schnell erstellt und ständig aktualisiert werden.
Belotti Integrale ist eine der ersten Anwendungen weltweit, die Robotik und CNC integriert: Die Roboter werden nämlich über die Sinumerik Integrate Run MyRobot-Funktionalität von der numerischen Steuerung von Siemens gesteuert, so dass der Kunde den Roboter mit der für Werkzeugmaschinen typischen klassischen ISO-Sprache programmieren kann. Ermöglicht wurde dies durch die Zusammenarbeit von zwei weltweit führenden Unternehmen wie KUKA und Siemens. Die Definition einer Schnittstelle, die den Datenaustausch zwischen den beiden Systemen ermöglicht. So kann die Siemens Sinumerik CNC perfekt mit der KUKA-Steuerungssoftware für die Robotersteuerung kommunizieren. Dies, war die ideale Lösung für die Integration von CNC-Technologie und Robotern: eine intelligente Automatisierungslösung, von der der Kunde voll profitiert.
Kontaktieren sie uns für weitere technische Informationen, Verkaufsanfragen oder um ein Online-Meeting zu vereinbaren.
Kontaktieren Sie uns für Produktinformationen, technische Unterstützung oder Ersatzeilanfragen.